Big machine tools and universal milling-boring machines are equipped with specific electrohydraulic systems to counterbalance the weight of the saddle and spindle during the vertical displacements, thus permitting the electromechanical driving unit to perform smooth and accurate motion controls.
Two different hydraulic solutions are commonly used for the counterbalance function: active circuit with power unit or closed circuit with accumulators.
In active solution, the 3-ways high performance pressure reducing valves with on board digital electronics perform an accurate closed loop pressure control in the counterbalance hydraulic cylinders thanks to the built-in pressure transducer installed on valve pressure ports.
Hydraulic cylinders for milling machines
Advantage of G9 seals and hydraulic system solutions to prevent stick-slip effect

The optimization of the performance in machine tools can be penalized by the stick-slip effect, the G9 sealing system represents the ideal solution that eliminates the phenomenon both in hydraulic system with active circuit and with closed circuit with accumulator.
INDEX
Counterbalance hydraulic solutions: active circuit and closed circuit
What’s the stick-slip in hydraulic cylinders?
Advantages of G9 special piston seals
Contact Us
Counterbalance hydraulic solutions: active circuit and closed circuit
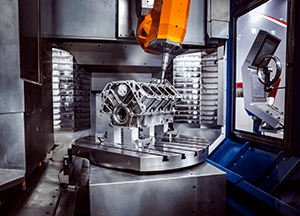
This high-performance solution requires a power unit equipped with a variable displacement piston pump to generate the line pressure.
The Atos Smart tuning feature allows the valve’s dynamic behaviour optimization to make pressure regulation stable and precise, even with continuous headstock load variations, with response times lower than 15 ms.
The closed circuit solution with accumulators is commonly used in highspeed counterbalance hydraulic systems, exploiting the ability of accumulators to store and release large volumes of fluid with low pressure variations.
This solution operates with low power supply and requires a PED certified safety control block, which integrates auxiliary functions such as shutoff valve, pressure gauge, leak free pressure relief valve and manual override.
The Atos Smart tuning feature allows the valve’s dynamic behaviour optimization to make pressure regulation stable and precise, even with continuous headstock load variations, with response times lower than 15 ms.
The closed circuit solution with accumulators is commonly used in highspeed counterbalance hydraulic systems, exploiting the ability of accumulators to store and release large volumes of fluid with low pressure variations.
This solution operates with low power supply and requires a PED certified safety control block, which integrates auxiliary functions such as shutoff valve, pressure gauge, leak free pressure relief valve and manual override.
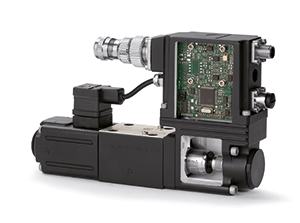
What’s the stick-slip in hydraulic cylinders?
In machine tool counterweight systems, the most common issue is the stick-slip effect, i.e. sticking between the cylinder seal and sliding surfaces.
This phenomenon generally triggers a vibration in the hydraulic system during the initial phase of the rod movement, due to the transition from static friction which opposes surfaces relative movement, to the dynamic friction generated by the surfaces sliding.
The stick-slip causes are attributed to the microstructures of the cylinder housing surfaces and by intermolecular forces between the sliding elements. In addition, the stick-slip effect generally leads to an increased wear of seals’ compound.
This phenomenon generally triggers a vibration in the hydraulic system during the initial phase of the rod movement, due to the transition from static friction which opposes surfaces relative movement, to the dynamic friction generated by the surfaces sliding.
The stick-slip causes are attributed to the microstructures of the cylinder housing surfaces and by intermolecular forces between the sliding elements. In addition, the stick-slip effect generally leads to an increased wear of seals’ compound.
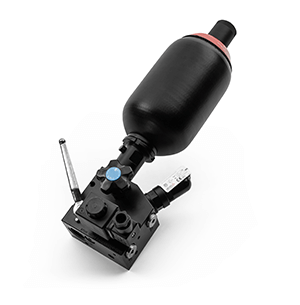
Advantages of G9 special piston seals
Atos R&D developed the G9 sealing system by conducting software and test bench simulations, as well as performing targeted collaborations with suppliers and major European OEMs to test its effectiveness in the field.
Collaboration with specialised suppliers enabled the identification of an innovative polymeric compound that drastically reduces the gap between static and dynamic friction coefficients, effectively eliminating the issues induced by the stick-slip phenomenon. As a result, the absence of vibration in the motion phase also translates into a longer cylinder operating life.
Tests carried out in the field have shown that in addition to the increase in dynamic performance, due to the very low friction forces of this solution, the efficiency of the vertical motor on the milling head also increases, as a consequence of the reduction in power consumption.
The G9 system features a single-acting seal with a special sealing lip geometry that guarantees zero leakage over the entire operating range.
Collaboration with specialised suppliers enabled the identification of an innovative polymeric compound that drastically reduces the gap between static and dynamic friction coefficients, effectively eliminating the issues induced by the stick-slip phenomenon. As a result, the absence of vibration in the motion phase also translates into a longer cylinder operating life.
Tests carried out in the field have shown that in addition to the increase in dynamic performance, due to the very low friction forces of this solution, the efficiency of the vertical motor on the milling head also increases, as a consequence of the reduction in power consumption.
The G9 system features a single-acting seal with a special sealing lip geometry that guarantees zero leakage over the entire operating range.
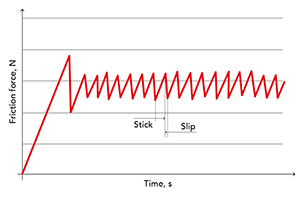
The zero leakage is a particular advantage in closed-circuit systems with accumulator, as it avoids continuous oil refilling in the counterweight system.
In addition, the G9 sealing system prevents the milling head from descending in absence of electrical power, unlike conventional sealing systems where leakage can cause the milling head to descend slowly.
More generally, the robust design of the seal, without the energized O-ring, stabilises the seal in its groove by preventing it from tilting, while the lip design eliminates issues associated with low-pressure sealing and provides additional stability in dynamics of the hydraulic system.
Atos hydraulic cylinders with the G9 sealing system are the preferred choice of many milling machine manufacturers around the world, who appreciate their performance and reliability, the result of years of R&D and successful field experiences.
In addition, the G9 sealing system prevents the milling head from descending in absence of electrical power, unlike conventional sealing systems where leakage can cause the milling head to descend slowly.
More generally, the robust design of the seal, without the energized O-ring, stabilises the seal in its groove by preventing it from tilting, while the lip design eliminates issues associated with low-pressure sealing and provides additional stability in dynamics of the hydraulic system.
Atos hydraulic cylinders with the G9 sealing system are the preferred choice of many milling machine manufacturers around the world, who appreciate their performance and reliability, the result of years of R&D and successful field experiences.
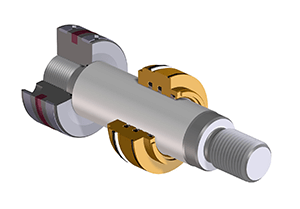
Contact us
Are you interested in Atos hydraulic cylinders?
Do not hesitate to contact us!
Follow us on LinkedIn to stay updated on our activities and products.
Do not hesitate to contact us!
Follow us on LinkedIn to stay updated on our activities and products.