The constant increase in the cost of energy and world’s growing awareness of energy saving are pushing towards ever more efficient and performant processes. Therefore, inductive technology is becoming more and more
popular in the most common applications. For example, just think that in our homes the induction hobs are replacing the common gas cooktops.
Magnetic induction allows energy to be transferred safely and efficiently from a coil to a load consisting of a ferromagnetic material; the energy transferred to the load is transformed into heat generated inside the metal itself. The direct transfer of energy within the metal maximizes heating performance compared to any other method, reducing heating time and minimizing energy waste.
Plastic machineries: the energy saving heating revolution
Inductive energy saving technology for extruders, injection molding and blow molding machines
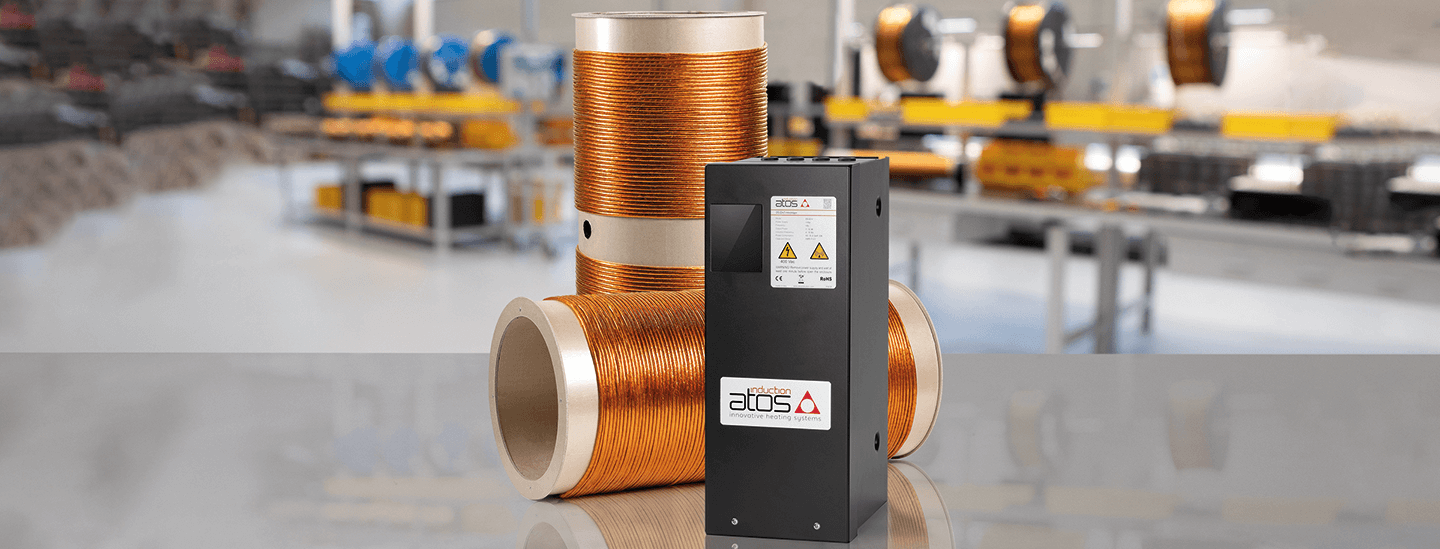
The technological evolution of heating in industrial processes involves the replacement of obsolete dissipative systems (resistors) with advanced energy saving solutions. Inductive extruders and plasticizing barrels revolutionize the plastic machines increasing productivity and efficiency, reducing operating and maintenance costs.
INDEX
The principle of electromagnetic induction
Induction technology for plastic machinery
Inductive energy saving solutions
Contact Us
The principle of electromagnetic induction

extruder plasticizing barrel
Induction technology for plastic machinery
Atos Induction has exploited the benefits of magnetic induction to create an innovative heating solution dedicated
to one of the most widespread industrial processes: plasticizing systems.
Inductive technology applied to plasticizing barrels offers multiple advantages over traditional resistive heating systems:
Typical application is composed by one or more coils, depending on the number of barrel zones to be heated, where each coil is powered by an electronic power generator. The customer’s machine central unit manages thermoregulation of each single zone, enabling or disabling the relevant power generator according to temperature feedbacks.
Inductive technology applied to plasticizing barrels offers multiple advantages over traditional resistive heating systems:
- Energy saving up to 30% on heating energy consumption
- Uniform heat distribution
- 30% less of installed electrical power respect equivalent machine with resistors
- Very fast heating, less than half time if compared to resistors
- High precision of temperature control, thanks to the absence of thermal inertia and instantaneous heat transfer of inductive technology
- Long operating life due to the reduced thermal stresses of the inductive coil
Typical application is composed by one or more coils, depending on the number of barrel zones to be heated, where each coil is powered by an electronic power generator. The customer’s machine central unit manages thermoregulation of each single zone, enabling or disabling the relevant power generator according to temperature feedbacks.
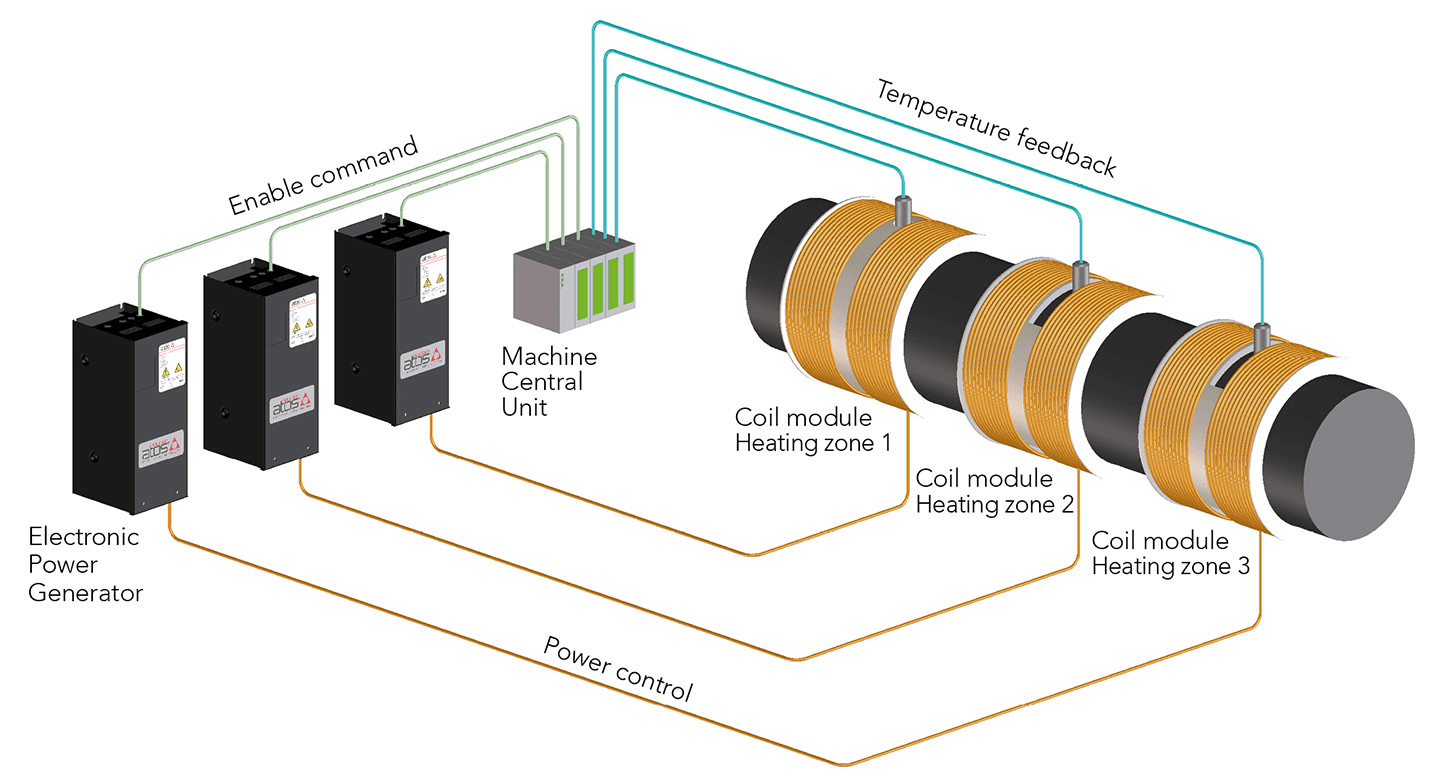
plastic injection machine or inductive
extruders machine
The electronic power generator self-adapts the current modulation according to the characteristics of the ferromagnetic material to be heated, in order to achieve the maximum efficiency in any working condition.
Inductive coil is wound on highly insulating materials to minimize heat loss from the barrel to the environment.
When a large area of the plasticizing cylinder operates at a single temperature, inductive coils allow a simplification of the machine control scheme and a reduction of the installed electrical components, since a single coil can cover lengths up to 700 mm.
When a large area of the plasticizing cylinder operates at a single temperature, inductive coils allow a simplification of the machine control scheme and a reduction of the installed electrical components, since a single coil can cover lengths up to 700 mm.
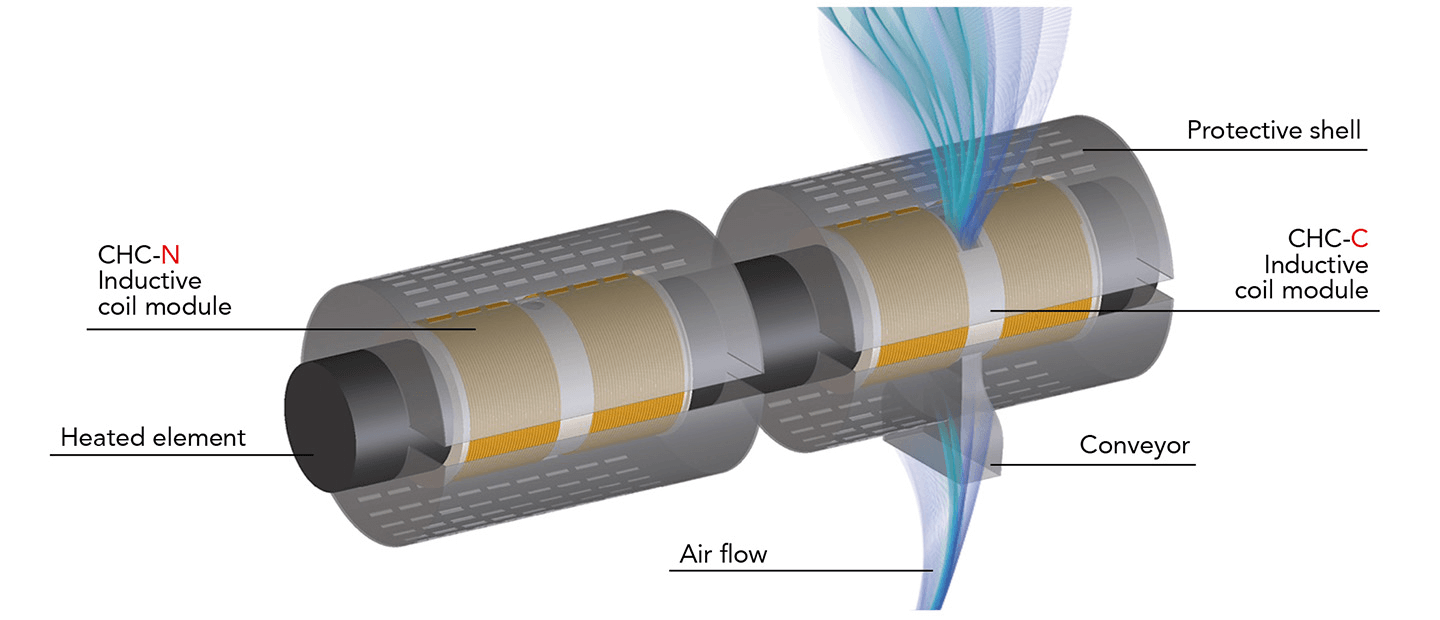
The modular construction technology of the inductive coils allows an easy installation on both cooled and uncooled plasticizing barrels:
- CHC-N coils are designed for temperature sensor installation and are suitable for those zones of the plasticizing barrel that do not require cooling
- CHC-C coils are provided with openings for airflow and temperature sensor installation. The special internal structure allows cooling air to be conveyed directly over the plasticizing barrel, guaranteeing faster cooling than resistive systems.
Inductive energy saving solutions
The focus on environmental pollution and the current escalation of energy prices is driving markets towards more efficient technologies and solutions.
Comparative analyses, performed on a 300 tons plastic injection machine, revealed that the energy consumption of inductive coils has been lower than 30% with respect to ceramic resistors, leading to annual savings of 28 MWh.
Atos Induction provides the energy saving technologies to equip the new generation of induction plastic injection and inductive extruders machines.
Comparative analyses, performed on a 300 tons plastic injection machine, revealed that the energy consumption of inductive coils has been lower than 30% with respect to ceramic resistors, leading to annual savings of 28 MWh.
Atos Induction provides the energy saving technologies to equip the new generation of induction plastic injection and inductive extruders machines.

300 ton plastic injection machine comparative analyses
Contact us
Are you interested in Atos Induction solutions?
Do not hesitate to contact us!
Follow us on LinkedIn to stay updated on our activities and products.
Do not hesitate to contact us!
Follow us on LinkedIn to stay updated on our activities and products.